[十年]水泥及礦渣微粉高效粉磨工藝探討
摘要:本文以大量工業(yè)生產(chǎn)及實驗數(shù)據(jù)探討了傳統(tǒng)的水泥及礦渣微粉粉磨工藝與高效節(jié)能的“料床粉磨工藝”的比較,認為:目前應(yīng)用廣泛的擠壓聯(lián)合粉磨工藝將會逐步向立磨粉磨工藝過渡。
關(guān)鍵詞:料床粉磨 立磨 輥壓機 筒輥磨
導(dǎo)言
自1883年磨機問世以來,已被廣泛用于水泥及其它行業(yè)的物料粉磨,在目前仍占有主導(dǎo)地位。傳統(tǒng)的水泥及礦渣微粉制備多采用管磨機粉磨工藝,由于其粉磨空間開放、四周不限,無法形成穩(wěn)定的料床,故粉磨效率低、單位粉磨電耗高、粉磨成本高。
隨著科學技術(shù)的快速進步,以粉磨時間短、粒度均勻的“料床粉磨”技術(shù)為代表的高效低能耗粉磨工藝及設(shè)備已成為當今水泥工業(yè)粉磨技術(shù)發(fā)展的主流。輥壓機、立磨、筒輥磨等高效率料床粉磨設(shè)備,正在逐步取代傳統(tǒng)的管磨機,用于水泥生產(chǎn)線中的生料、煤粉制備及水泥、礦渣微粉的終粉磨,并獲得了良好的技術(shù)經(jīng)濟效果。
本文探討了水泥及礦渣微粉傳統(tǒng)粉磨工藝與料床粉磨工藝的比較,文中不妥之處,懇望各位同仁予以批評指正。
不同粉磨工藝及其特點比較
如前所述,以管磨機為代表的傳統(tǒng)粉磨工藝,已有一百多年歷史,粉磨過程將電能轉(zhuǎn)化為機械能的同時,產(chǎn)生的聲和熱,消耗了大量電能,導(dǎo)致單位產(chǎn)品電耗居高不下,尤其是當入磨物料粒度大、易磨性差或水份大時,磨機粉磨效率顯著降低,更加劇了這一惡性循環(huán)。所以,管磨機在水泥工業(yè)中的應(yīng)用已受到高效能料床粉磨設(shè)備的挑戰(zhàn),并將會逐步退出粉磨領(lǐng)域。
表1 管磨機與立磨、輥壓機、筒輥磨粉磨特性對比
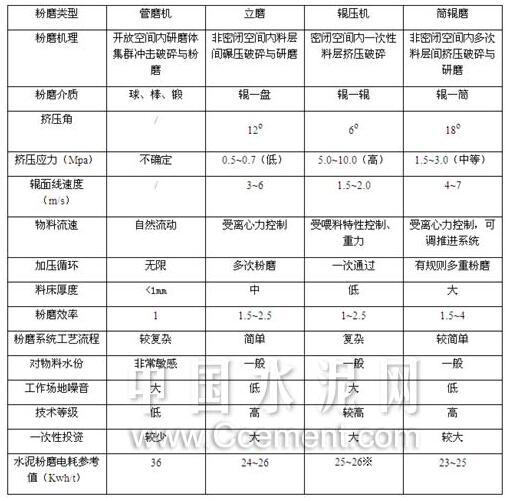
※指聯(lián)合粉磨系統(tǒng)電耗;輥壓機終粉磨電耗在21~22Kwh/t;
從表1中數(shù)據(jù)分析認為:采用料床粉磨設(shè)備終粉磨水泥(或礦渣)時,其電耗基本相當,但比管磨機系統(tǒng)節(jié)電約30%以上,除輥壓機工藝系統(tǒng)較為復(fù)雜外,立磨與筒輥磨工藝系統(tǒng)比管磨機系統(tǒng)更簡單些。
從目前國內(nèi)新建的新型干法水泥生產(chǎn)線來看,大多數(shù)生料制備系統(tǒng)采用立磨工藝,單位粉磨電耗<15kwh/t;同時,立磨自身集烘干、破碎、粉磨、選粉、收集、輸送功能于一體、占地面積小、粉磨效率高、電耗低且運行穩(wěn)定而成為首選機型。輥壓機用于生料終粉磨,單位電耗低于立磨,因系統(tǒng)復(fù)雜程度及技術(shù)含量高,維護管理工作量大,國內(nèi)采用的廠家極少。筒輥磨多用于水泥粉磨系統(tǒng),但國內(nèi)應(yīng)用廠家也很少。
采用料床粉磨工藝終粉磨產(chǎn)品性能
就當前而言,立磨、輥壓機、筒輥磨三種料床粉磨設(shè)備都可以用于水泥及礦渣微粉的終粉磨?,F(xiàn)以立磨為例,世界各知名公司的立磨都有其自主知識產(chǎn)權(quán),磨機內(nèi)部結(jié)構(gòu)不盡相同、各有千秋。國外立磨結(jié)構(gòu)形式見表2:
表2 國外立磨基本結(jié)構(gòu)形式
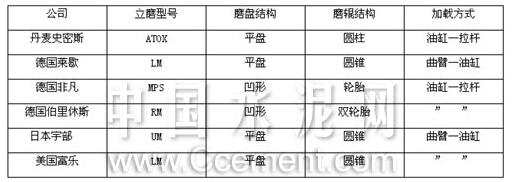
國內(nèi)天津院、合肥院及中信重機、沈重等科研院所及大形設(shè)備制造廠家都推出了各自研發(fā)的立磨并應(yīng)用于新型干法水泥生產(chǎn)線,近悉:天津院的TRM5341立磨成功用于遼寧富山5000t/d線生料系統(tǒng)、合肥院的HRM4800立磨成功用于浙江虎山集團5000t/d線生料制備,前幾年沈重生產(chǎn)的MLS4531立磨用于銅陵海螺
(228.3元/噸,-0.43%)5000t/d線磨制生料、中信重機也推出了LGMS4624立磨(磨制礦渣粉為90t/h、粉磨水泥熟料為120t/h)等,標志著我國大型水泥粉磨設(shè)備的研發(fā)、制造能力已同步于世界先進水平。
料床粉磨技術(shù)發(fā)展過程中,尤其在水泥終粉磨初期,曾經(jīng)遇到磨細后的水泥成品,顆粒級配范圍窄、均勻性系數(shù)大、標準稠度需水量大、凝結(jié)時間過快等,立磨和輥壓機的終粉磨均經(jīng)歷過此現(xiàn)象。筒輥磨問世較晚,在研發(fā)過程中鑒于前兩種設(shè)備終粉磨出現(xiàn)的問題,在生產(chǎn)中加大了循環(huán)量,并通過調(diào)節(jié)其他工藝參數(shù),較好地解決了這些問題。
墨西哥某廠采用Polysuis RMC-51/26立磨配用Sepol RMC435高效選粉機磨制純硅酸鹽水泥,系統(tǒng)電耗25.2Kwh/t,比閉路磨系統(tǒng)節(jié)電50%以上,水泥質(zhì)量良好。
表3 水泥性能檢測結(jié)果

FLS公司引進小野田和神戶制鋼聯(lián)合開發(fā)并改進的OK立磨廣泛用于粉磨水泥及礦渣微粉,其磨輥呈曲面,帶曲面凹槽的磨盤及磨輥在粉磨過程中可及時排出料床中的壓縮空氣,穩(wěn)定料床及減少磨振。檢修時,磨輥可通過操作磨體外油缸將其翻至磨外,便于維護。
表4 臺灣某廠OK19-3立磨生產(chǎn)的水泥性能
表中數(shù)據(jù)說明:在凝結(jié)時間、標準稠度需水量基本相同的前提下,OK磨磨制的水泥28d抗壓強度比球磨水泥高出15%,同時,水泥的早期強度也高,可進一步增加混合材摻量,降低水泥生產(chǎn)成本。
OK磨工作時,可通過調(diào)節(jié)磨盤轉(zhuǎn)速、輥壓、選粉機轉(zhuǎn)速、氣流速度及磨內(nèi)擋料圈高度等工藝技術(shù)參數(shù)達到調(diào)節(jié)水泥顆粒級配的目的,操作非常方便。采用OK磨制備比表面積400~500m
2/kg礦渣微粉時,與管磨機系統(tǒng)相比,OK磨粉磨電耗降低35~45%,節(jié)能潛力巨大,生產(chǎn)成本顯著下降。
國內(nèi)某公司采用進口立磨粉磨新型干法窯熟料制備不同強度等級的水泥,其實物質(zhì)量數(shù)據(jù)見表5:
表5 立磨生產(chǎn)的水泥質(zhì)量檢測結(jié)果
表5數(shù)據(jù)進一步證實了國內(nèi)現(xiàn)階段采用立磨終粉磨,已解決了水泥標準稠度需水量過大、顆粒級配范圍窄(均勻性系數(shù)n值偏大)等相關(guān)技術(shù)問題。
關(guān)于礦渣微粉粉磨工藝
隨著高性能混凝土技術(shù)的發(fā)展與應(yīng)用,礦渣微粉已成為混凝土制備中不可或缺的第六組分材料(人工礦物摻合料)。?;郀t礦渣系冶煉生鐵時排出的工業(yè)廢渣,每生產(chǎn)一噸生鐵,大約排出300~1000kg礦渣,其礦物成份在Cao-Sio2-Al2o3三元相圖中處于C2AS、CAS2、CS、C2S結(jié)晶區(qū),大致化學成份為CaO34~46%、SiO222~40%、Al2O35~15、MgO2~13%,并含有少量FeO、MnO、S及TiO2和金屬鐵。礦渣出爐時經(jīng)水淬急冷,保留了微晶態(tài)的高活性玻璃體結(jié)構(gòu),其有較高的潛在物理化學活性,在含有硫、堿成份的水化環(huán)境中可激發(fā)出良好的水硬活性(如前蘇聯(lián)研究的堿-礦渣高強水泥屬此類),可將礦渣看作是一種經(jīng)過高溫煅燒的高硅、低鈣熟料。礦渣采用機械力活化,磨細制得的微米級粉體,具有潛在水硬性礦物的晶格產(chǎn)生畸變,發(fā)揮出優(yōu)良的水化膠凝活性。磨細礦渣微粉摻入水泥中的強度試驗結(jié)果見表6:
表6 磨細礦渣微粉摻入水泥中的膠砂強度
由表6數(shù)據(jù)可以看出:在含有礦渣配比20%的425礦渣水泥中摻入磨細礦渣微粉取代等量水泥后,水泥的早、后期強度非但沒有降低,反而有顯著的提高,充分說明磨細礦渣微粉具有優(yōu)良的潛在水硬活性,在水泥生產(chǎn)過程中對改善產(chǎn)品的物理力學性能具有重要意義。近年來,磨細礦渣微粉作為高活性礦物摻合料,已廣泛應(yīng)用于高性能、高強混凝土,并對其技術(shù)機理的研究逐步微觀化、系統(tǒng)化、深入化。不同比表面積磨細礦渣微粉應(yīng)用于混凝土中的試驗數(shù)據(jù)見表7:
表7 不同比表面積礦渣粉砼的物理性能
由表7可知:在水泥用量基本相同的混凝土中,當?shù)V渣微粉的摻入量也基本相同時,混凝土的強度隨礦渣微粉比表面積的提高而提高。
摻有磨細礦渣微粉的水泥及混凝土具有優(yōu)良的抗?jié)B性能和抗硫酸鹽侵蝕性能,后期增進率高,大幅度提高了水泥石及混凝土的致密程度,尤其適用于潮濕環(huán)境中及大體積水工混凝土的制備。國外,在海工混凝土配制過程中就大量摻用磨細礦渣微粉,可以顯著提高混凝土抵抗有害化學離子侵蝕能力及混凝土的耐久性與使用壽命。當磨細礦渣微粉取代等量水泥摻入混凝土后,混凝土水化體系放熱明顯減少,內(nèi)、外部溫差進一步縮小,降低了混凝土產(chǎn)生開裂的機率。同時,由于整個水化體系中堿含量降低,為有效防止混凝土堿-骨料反應(yīng)(AAR)的發(fā)生創(chuàng)造了良好的先決條件。
礦渣微觀屬高活性玻璃體結(jié)構(gòu),顯微硬度大(HV650左右)、韌性好、易磨性差,即易碎難磨細。采用管磨機粉磨工藝制備的比表面積≥430m
2/kg礦渣微粉時,不僅單位粉磨電耗>70kWh/t,而且研磨體消耗量大,以中鉻合金材質(zhì)研磨體為例,噸礦渣粉的球、鍛磨耗>250-300g/t,如采用φ3.2×13m開流管磨機,磨機主電機功率為1600kW,生產(chǎn)比表面積≥430m2/kg礦渣微粉,臺時產(chǎn)量也只有28t/h左右,單位粉磨電耗達72kWh/t,生產(chǎn)成本明顯高于立磨。
近年來,國內(nèi)建設(shè)的大型礦渣微粉生產(chǎn)線,如長鋼瑞昌、萊鋼魯碧、四川
星船城等均采用了萊歇立磨粉磨工藝。如前所述,立磨集烘干、破碎、粉磨、選粉、收集、輸送功能于一體,占地面積少,大大簡化了生產(chǎn)線工藝布置。據(jù)了解,這些立磨生產(chǎn)線的單機產(chǎn)量一般都在150t/h以上,礦渣微粉比表面積≥450m
2/kg,單位粉磨電耗<50 kWh/t,甚至<45kWh/t ,而且磨耗也遠低于管磨機系統(tǒng),節(jié)電幅度>30%。
國內(nèi)由天津院研制開發(fā)的第一臺礦渣磨TRM3131S,用于杭州紫恒公司制備礦渣微粉,配用高效籠式選粉機,成品細度可在400~600m
2/kg范圍內(nèi)靈活調(diào)節(jié),當控制礦渣微粉比表面積450m
2/kg時,立磨臺時產(chǎn)量達52t/h,系統(tǒng)電耗為37.3kWh/t,制備的礦渣微粉性能見表8:
表8 TRM3131S立磨生產(chǎn)的礦渣微粉性能
以上事實證明:無論水泥及礦渣微粉的制備過程,傳統(tǒng)的粉磨工藝將逐步向料床粉磨工藝過渡,立磨、輥壓機、筒輥磨等高效粉磨設(shè)備,必將在不同場合取代現(xiàn)行管磨機,具有廣闊的增產(chǎn)、節(jié)電前景。
擠壓聯(lián)合粉磨和筒輥磨系統(tǒng)
在輥壓及問世之初,主要用于預(yù)粉磨流程,其功效尚不能完全發(fā)揮,加之輥壓機自身存在一定的技術(shù)缺陷:輥面磨損過快、液壓系統(tǒng)泄漏、邊緣效應(yīng)等,經(jīng)過二十余年的發(fā)展改進以及新材料、新技術(shù)的應(yīng)用,輥壓機的技術(shù)性能不斷得到完善,現(xiàn)階段輥壓機輥面工作壽命可達20000h以上,其他方面的問題也迎刃而解。
輥壓機作為終粉磨設(shè)備,其電耗較低,比球磨系統(tǒng)節(jié)電30%以上。但存在水泥顆粒級配范圍過窄、均勻性系數(shù)n值偏大、水泥凝結(jié)時間過快(石膏分布不均勻緩凝效果差所致)、成品顆粒形貌為多角形結(jié)構(gòu),導(dǎo)致水泥標準稠度需水量過大等。采用擠壓聯(lián)合粉磨工藝,主要是充分發(fā)揮輥壓機的預(yù)粉磨功能,必須使輥壓機多做功,才能增加擠壓料中細粉的含量,輥壓機多做功1kwh,后續(xù)管磨機可節(jié)省2-3kwh,管磨機能夠真正發(fā)揮其特有的研磨功能,在使系統(tǒng)獲得高產(chǎn)低耗的同時,對入磨粗粉水泥的多角形結(jié)構(gòu)顆粒進行“整形”,改善水泥的顆粒級配,降低需水性,以確保提高水泥的使用性能。
采用擠壓聯(lián)合粉磨工藝可在原粉磨系統(tǒng)基礎(chǔ)上增產(chǎn)50~150%,單位粉磨電耗較普通管磨機粉磨工藝可節(jié)省30%以上。擠壓聯(lián)合粉磨系統(tǒng)的后續(xù)管磨機有開流和圈流兩種形式,同一企業(yè)采用擠壓聯(lián)合粉磨工藝,后續(xù)均為φ3.2×13m管磨機,開流、圈流兩種不同系統(tǒng)制備的水泥性能見表9:
表9 擠壓聯(lián)合粉磨系統(tǒng)水泥質(zhì)量檢測結(jié)果
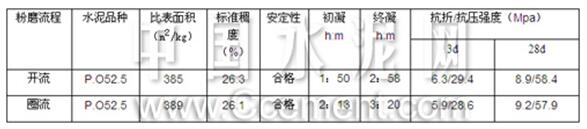
從表9得知,在相同熟料配比條件下,采用擠壓聯(lián)合粉磨工藝后續(xù)管磨機為開流系統(tǒng)時,所磨制的強度等級P.O52.5水泥早、后期強度略高于圈流系統(tǒng)粉磨的水泥。同時,凝結(jié)時間也要短些,水泥顆粒級配范圍更寬些,開流系統(tǒng)單位粉磨電耗為25.7Kwh/t,圈流系統(tǒng)單位粉磨電耗為27.4Kwh/t。此外,圈流系統(tǒng)工藝略復(fù)雜些,這也許是部分企業(yè)選用開流粉磨工藝的真正原因。
國內(nèi)牡丹江水泥公司2003年引進法國FCB公司研制的HoRo mill3800筒輥磨用于粉磨水泥(國內(nèi)第一臺應(yīng)用),裝機功率2400kw,配用TSV4500選粉機,設(shè)計能力120t/h,輥筒工作轉(zhuǎn)速36r/min,單位粉磨電耗為24.5kwh/t。筒輥磨生產(chǎn)的水泥與球磨磨制的水泥物理性能對比見表10:
表10 筒輥磨與球磨磨制的水泥性能對比
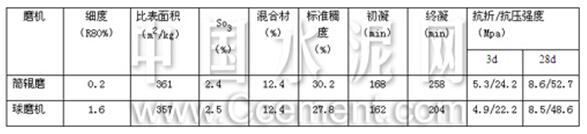
表中數(shù)據(jù)可以看出:相同混合材配比條件下,與球磨水泥相比,筒輥磨磨制備的水泥有更高的早、后期強度,與立磨磨制的水泥性能基本相似,說明仍能進一步提高混合材摻量,降低生產(chǎn)成本。筒輥磨單位粉磨電耗比立磨更低些,顯示出其特有的技術(shù)優(yōu)勢。在水泥物理性能方面,筒輥磨生產(chǎn)的水泥標準稠度需水量仍略大于球磨機磨制的水泥,這可能是筒輥磨水泥顆粒形貌大部分為扁針狀,水化過程比球形顆粒更快的緣故。
結(jié)束語
5.1傳統(tǒng)的管磨機粉磨工藝,其粉磨空間四周不限,難以形成料床,故效率低、單位粉磨電耗高、研磨體消耗大、生產(chǎn)成本高。目前應(yīng)用廣泛的擠壓聯(lián)合粉磨系統(tǒng)部分引入了料床粉磨工藝,屬成熟的節(jié)能工藝技術(shù),但工藝系統(tǒng)布局較為復(fù)雜,隨著時間的推移,將會逐步向立磨終粉磨過渡。
5.2立磨、輥壓機、筒輥磨均為料床粉磨的高效節(jié)電設(shè)備,實現(xiàn)了無球化終粉磨,用于制備水泥和礦渣微粉,相對傳統(tǒng)管磨機粉磨工藝而言,節(jié)電幅度達30~40%以上,更有利于節(jié)能減排,發(fā)展循環(huán)經(jīng)濟,功在當代,利在千秋。
5.3立磨集烘干、破碎、粉磨、選粉、收集、輸送于一體,并已率先實現(xiàn)大型化,工藝流程簡單、占地面積小,單位粉磨電耗和金屬磨耗低,是當前大、中型水泥及礦渣微粉制備企業(yè)首選的高效粉磨工藝設(shè)備。
5.4立磨、筒輥磨與傳統(tǒng)管磨機粉磨工藝所制備的水泥力學性能相比,具有更高的早、后期強度,可以增加混合材摻加量、降低噸位水泥制造成本,綜合提高經(jīng)濟效益。同時,由于大量摻用工業(yè)廢渣,有利于凈化環(huán)境、消除廢渣污染。
5.5無論磨制水泥或礦渣微粉,要求磨前設(shè)置多道強力除鐵,由于單質(zhì)鐵粒具有鐵磁性和可塑性,難以磨細的同時在磨內(nèi)產(chǎn)生富集,加劇設(shè)備磨損,必須予以除去。以使粉磨系統(tǒng)保持較高而穩(wěn)定的粉磨效率,有效降低主機設(shè)備磨損,延長工作壽命。
說明:本文撰寫過程中,參考并引用了水泥界老師們著作中的部分數(shù)據(jù),在此向各位老師致以深深的謝意!
參考文獻
【1】.張路明,《國內(nèi)立磨發(fā)展概況及LGMS4626礦渣立磨的研制與使用》,《礦山機械》2008.3【2】.趙乃仁,《Polysuis立磨粉磨水泥》,《水泥工程》2004.3
【3】.熊會思、熊然《新型干法水泥廠設(shè)備選型使用手冊》,中國建材工業(yè)出版社2007年1月第一版
【4】. 柴星騰,《TRM礦渣輥磨的研制與應(yīng)用》,《中國建材報·機械與裝備》2008.5.20頭版
【5】. 任林燕,《Horomill與球磨機磨制的水泥性能對比》,《水泥》2004.6
摘自:中國建材工業(yè)經(jīng)濟研究會水泥專業(yè)委員會 鄒偉斌